Infrastrutture in acciaio
Perché infrastrutture in acciaio
La scelta del materiale da costruzione è fondamentale già nelle prime fasi di pianificazione di un’opera, nelle quali devono essere presi in considerazione molteplici aspetti: economici, estetici, ambientali.
L’acciaio, in un contesto tecnologico in continuo progresso, rappresenta la migliore soluzione costruttiva per la realizzazione delle infrastrutture, poiché possiede le caratteristiche più adatte a soddisfare le esigenze per questo tipo di opere.
Resistenza e leggerezza
Grazie alle proprietà meccaniche di cui gode, l’acciaio consente la realizzazione di strutture leggere e allo stesso tempo dotate di elevata resistenza e rigidezza. Un’attenta progettazione permette di ridurre non solo le azioni statiche derivanti dal peso proprio della struttura ma anche quelle dinamiche grazie alla moderata entità delle masse sismiche. Questi accorgimenti generano un netto risparmio in confronto con gli altri materiali da costruzione, in merito ai quantitativi di materiale da impiegare sulle spese per la realizzazione delle strutture di fondazione e per lo sbancamento. L’acciaio domina indiscutibilmente il panorama delle infrastrutture che coprono le grandi luci.
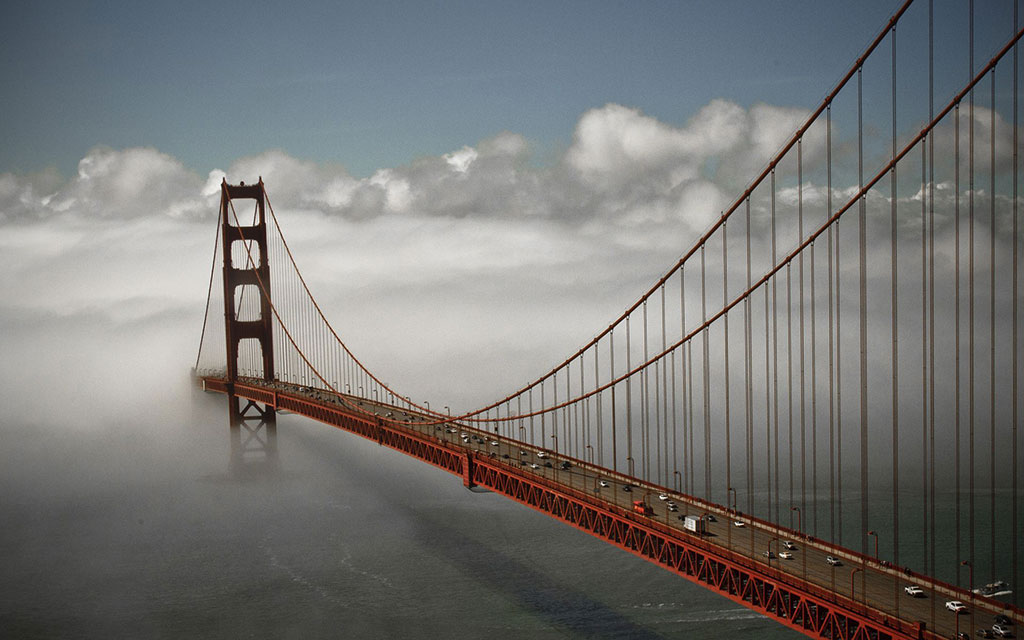
Golden Gate Bridge (1933-1937 - San Francisco, USA, luce totale: 2.737 m, campata max: 1.282 m)
Estetica
Il ponte può essere considerata la tipologia di opera in cui forma e struttura tendono a coincidere: per questo motivo risulta molto importante l’aspetto esteriore di un’infrastruttura. Durante la fase di progettazione è fondamentale considerare in quale contesto ambientale debba essere inserita l’opera, valutando attentamente l’impatto visivo. Le infrastrutture in acciaio sono particolarmente indicate anche per quegli interventi che devono essere effettuati in delicati contesti di tipo storico-culturale-ambientale. La snellezza delle opere in acciaio consente la migliore integrazione sia per gli interventi a basso impatto ambientale nei contesti naturalistici, sia per gli interventi “minimali” in quelli storici.
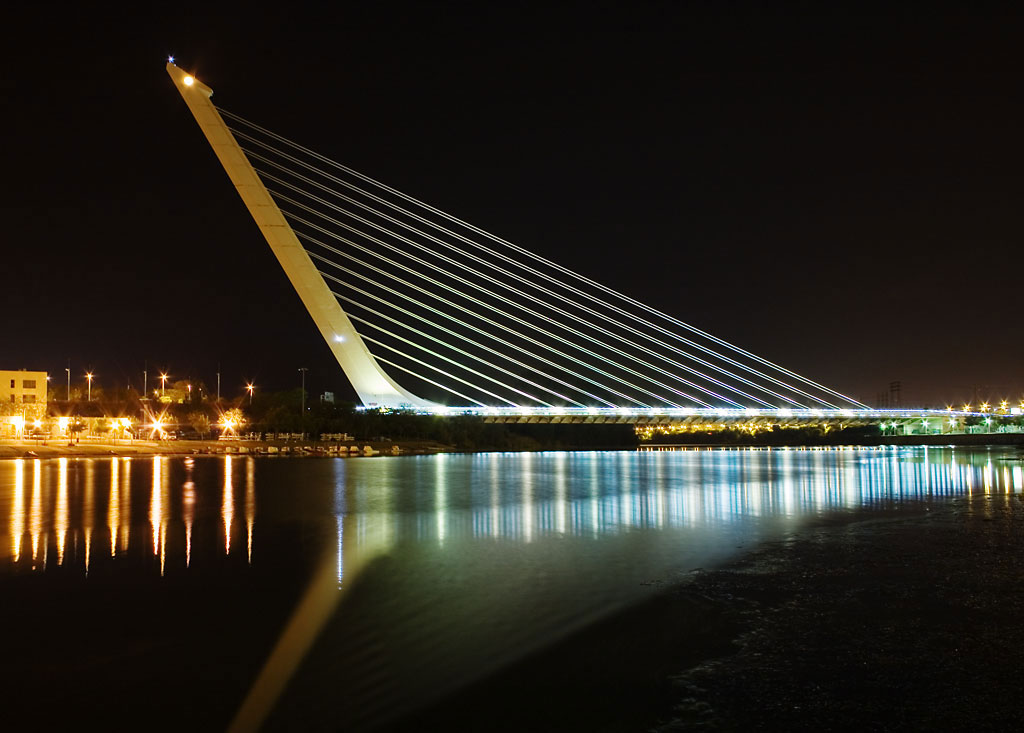
Alamillo Bridge (1992 - Siviglia, Spagna, campata max: 200 m)
Semplicità e velocità costruttiva
Un grande vantaggio delle strutture in acciaio è la preparazione in officina degli elementi costitutivi, che consente di ridurre il numero delle attività in cantiere e di conseguenza anche l’occupazione di suolo. Le operazioni previste in opera, infatti, sono limitate al solo montaggio dei componenti strutturali, il tutto a vantaggio di una maggiore velocità costruttiva. La costruzione off site è fondamentale nell’ambito delle infrastrutture, poiché permette una notevole riduzione dei tempi di cantierizzazione delle opere, consentendo pertanto di evitare interruzioni della viabilità protratte nel tempo, a favore di una riduzione dei costi di realizzazione. La lavorazione in officina degli elementi consente di affidarsi a maestranze specializzate; manodopera qualificata che garantisce inoltre un ottimale controllo delle attività svolte in cantiere, a totale beneficio della sicurezza.
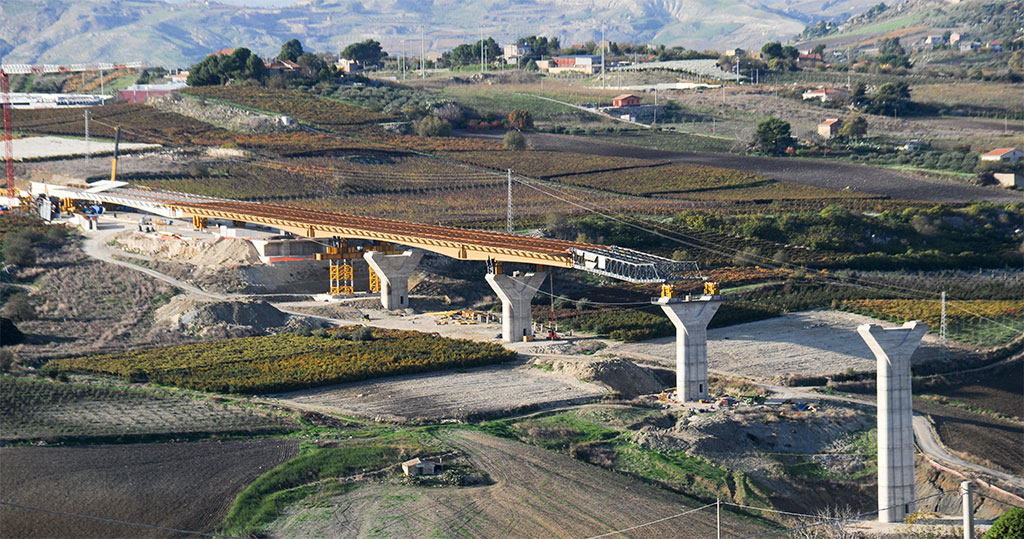
Viadotto Serra-Cazzola, fase di varo (2009-2013 – Castrofilippo-Canicattì AG, luce tot: 980 m, campata max: 120 m)
Qualità e durabilità
L’acciaio impiegato nelle opere in carpenteria metallica è sinonimo di qualità. Norme europee (ad esempio, la marcatura CE) regolano la tracciabilità ed il controllo dei prodotti a partire dalla produzione in acciaieria, passando dai processi di prima lavorazione da parte dei centri servizio / distributori fino alla prefabbricazione in officina e al montaggio in cantiere. Qualità intesa soprattutto come garanzia di prestazioni nel tempo e dunque di durabilità, tema di grandissima importanza nell’ambito delle infrastrutture perché legato ai costi di mantenimento. Grazie all’efficacia dei trattamenti effettuati sui prodotti (ad esempio la zincatura e/o la verniciatura) o l’uso di particolari qualità di acciai (ad esempio gli acciai autopatinabili o gli acciai inossidabili), è possibile proteggere il materiale dall’azione degli agenti atmosferici, rimandando e riducendo gli interventi di manutenzione delle infrastrutture in acciaio in maniera consistente durante la vita utile. Questo dato è fondamentale perché comporta vantaggi economici evidenti, poiché vengono abbattuti i costi di gestione delle opere, a garanzia di un investimento che dura nel tempo.
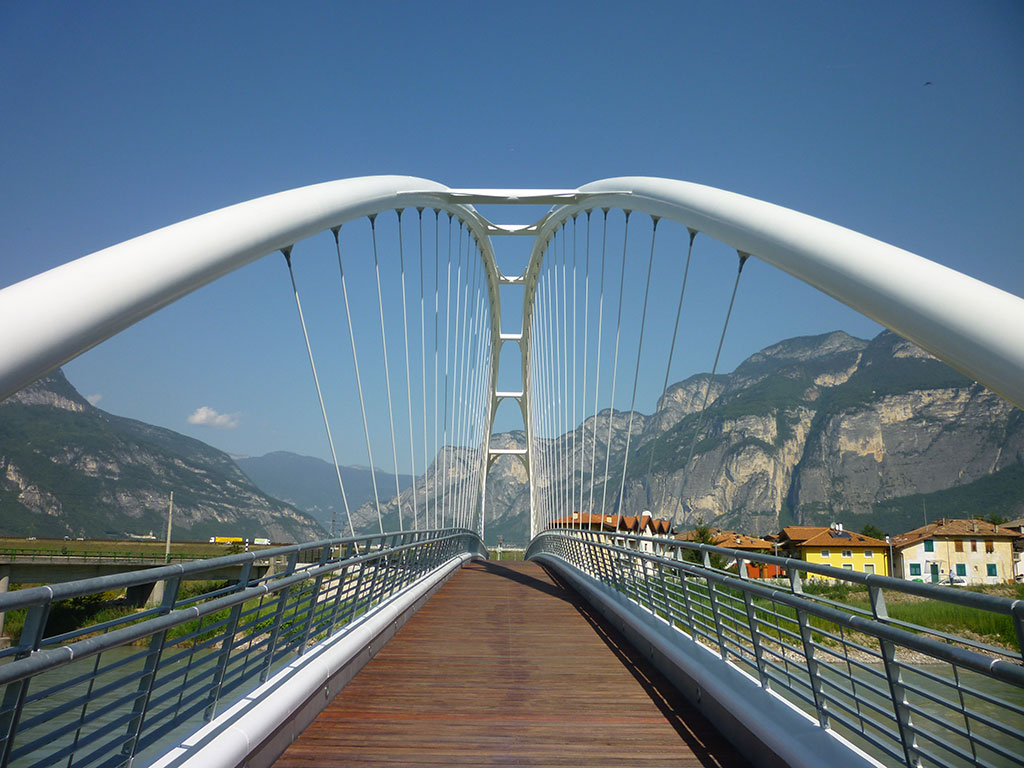
Ponte ciclopedonale San Michele all’Adige zincato e verniciato (2010 – San Michele all’Adige TN, campata max: 107 m)
Sostenibilità
L’acciaio è il materiale riciclabile per eccellenza. Al termine della vita utile di un’opera, l’acciaio dismesso può essere riciclato al 99%, il restante 1% viene recuperato come inerte per uso stradale. L’acciaio derivante dal riciclo è un materiale di prima scelta in quanto mantiene le stesse proprietà meccaniche di quello originale senza alcuna perdita di qualità, ciò ci consente di utilizzarlo più e più volte per la stessa applicazione. Questa caratteristica lo rende una vera e propria “risorsa permanente”, essenziale in una visione economica ti tipo circolare. La completa riciclabilità e la durabilità dell’acciaio permettono pertanto un minor consumo delle materie prime e di conseguenza uno sviluppo e una gestione economica delle infrastrutture più sostenibile in confronto a opere realizzate con altri materiali da costruzione.
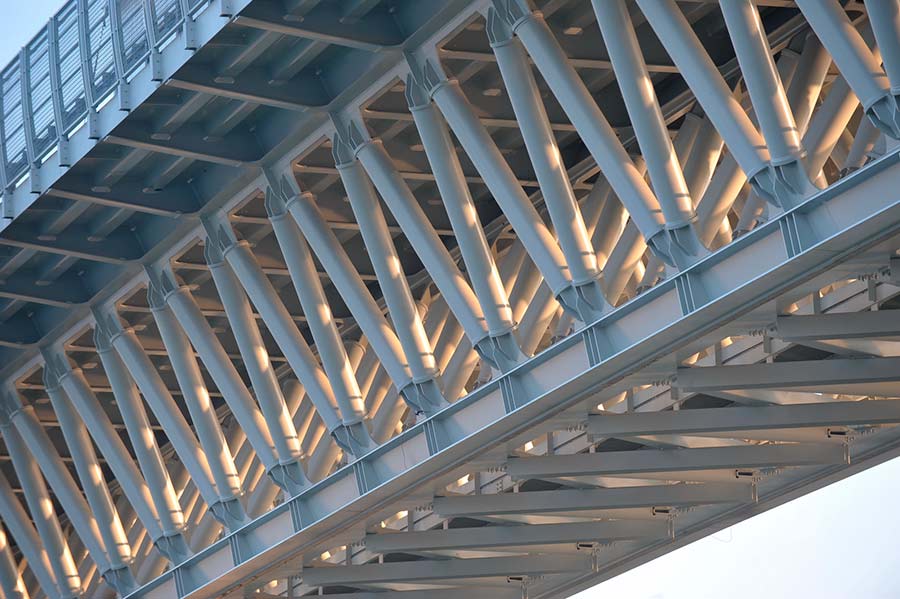
Ponte sul fiume Po – S.S.9, ricostruito riciclando tutto l’acciaio del ponte preesistente e certificato a livello internazionale come prodotto ambientale (2009-2010 – Lodi/Piacenza, luce totale: 814 m, campata max: 76 m)
Ponti, passerelle, viadotti e cavalcavia in acciaio
La realizzazione di un ponte nasce dall’esigenza dell’uomo di oltrepassare un ostacolo, naturale o artificiale, il quale costituisce una discontinuità solitamente per una via di comunicazione.
A seguire vengono presentati alcuni criteri di classificazione dei ponti, con un approfondimento dedicato alla loro identificazione in base allo schema statico.
Classificazione secondo l’ostacolo da superare
L’infrastruttura acquisisce propriamente il nome di ponte se l’ostacolo da superare è un corso d’acqua, quello di viadotto se costituito da una vallata o da una gola e, infine, quello di cavalcavia se rappresentato da un’altra via di comunicazione.
Classificazione secondo l’uso
I ponti possono anche essere classificati a seconda della tipologia del servizio: le opere finalizzate al transito di mezzi su ruote prendono il nome di ponti stradali, quelle deputate al transito di mezzi su rotaia prendono il nome di ponti ferroviari; nel caso l’infrastruttura preveda il solo passaggio di pedoni o ciclisti, essa acquisisce il nome di passerella pedonale o ciclopedonale.
Classificazione secondo lo schema statico
Premettendo che risulta complesso, addirittura forzato nel caso di sistemi ibridi, formulare una classificazione tipologica per i ponti in acciaio, vengono a seguire individuate quattro categorie principali in relazione allo schema statico: ponti ad arco, ponti a travata, ponti strallati e ponti sospesi.
Premettendo che risulta complesso, addirittura forzato nel caso di sistemi ibridi, formulare una classificazione tipologica per i ponti in acciaio, vengono a seguire individuate quattro categorie principali in relazione allo schema statico: ponti ad arco, ponti a travata, ponti strallati e ponti sospesi.
La scelta delle soluzioni tecnologiche dipende principalmente dalla distanza fra gli appoggi, che determina il peso delle strutture.
Per capire qual è la soluzione più efficiente da impiegare in funzione della luce, è possibile adottare un coefficiente di rendimento di un ponte Kst, definito come:
Le differenti soluzioni tecnologiche permettono di coprire luci differenti ottimizzando il valore del coefficiente di rendimento.
Di seguito si riporta un confronto fra luci limite dal punto di vista economico, le luci teoriche e le luci massime realizzate nel mondo al variare dello schema statico e del materiale utilizzato:
Ponti a travata
I ponti a trave, a travata o a telaio sono tipicamente usati per coprire luci minori e sono composti da uno o più sistemi di travi che sostengono l’impalcato seguendo differenti schemi resistenti.
I ponti composti da una trave o una serie di travi semplicemente appoggiate sulle pile e/o sulle spalle vengono impiegati per coprire luci minori. Presentano vantaggi tipici degli schemi isostatici, come ad esempio la semplicità nel calcolo e nella realizzazione e l’assenza di autotensioni indotte da diversi fenomeni, fra cui i cedimenti e i carichi termici. Tuttavia, necessitano di molti giunti e apparecchi d’appoggio a svantaggio di maggiori costi di manutenzione. Appartengono a questa categoria i ponti a Travata Gerber i quali migliorano lo sfruttamento del materiale grazie allo schema a cerniere interne che permette una distribuzione più uniforme delle sollecitazioni.
I ponti a trave o travata continua su più appoggi, al contrario, necessitano di pochi giunti e soprattutto sfruttano al meglio la resistenza dell’acciaio in campo plastico grazie alla configurazione iperstatica, introducendo nel calcolo gli effetti autoindotti dei carichi termici e dei cedimenti. Per i ponti a travata continua la soluzione oggi più diffusa è la sezione a cassone, che comporta molteplici vantaggi. Innanzitutto possiede una notevole capacità portante grazie all’elevata rigidezza e resistenza torsionale, diventando la soluzione ideale in caso di impalcati curvi e di carichi eccentrici. Grazie alla loro eleganza formale, inoltre, i ponti a cassone si inseriscono in modo gradevole nel paesaggio, diventandone un valore aggiunto.
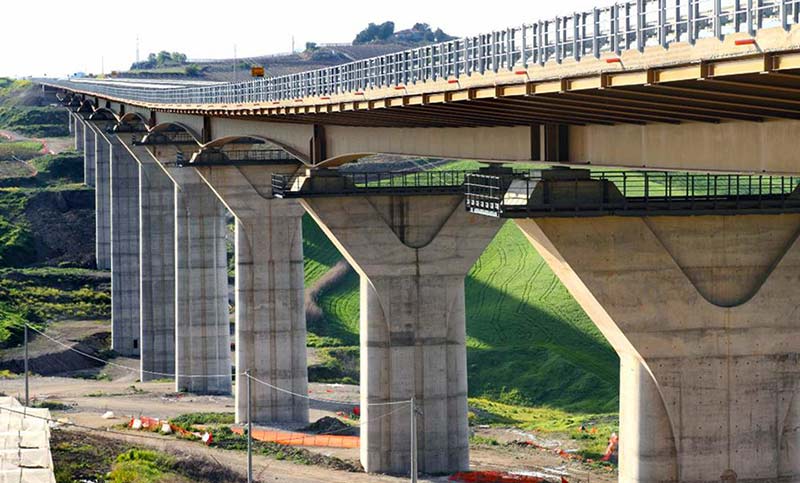
Esempio di viadotto a doppia travata continua su più appoggi: Viadotto Serra Cazzola (2009-2013 – Castrofilippo-Canicattì AG, luce tot: 980 m, campata max: 120 m
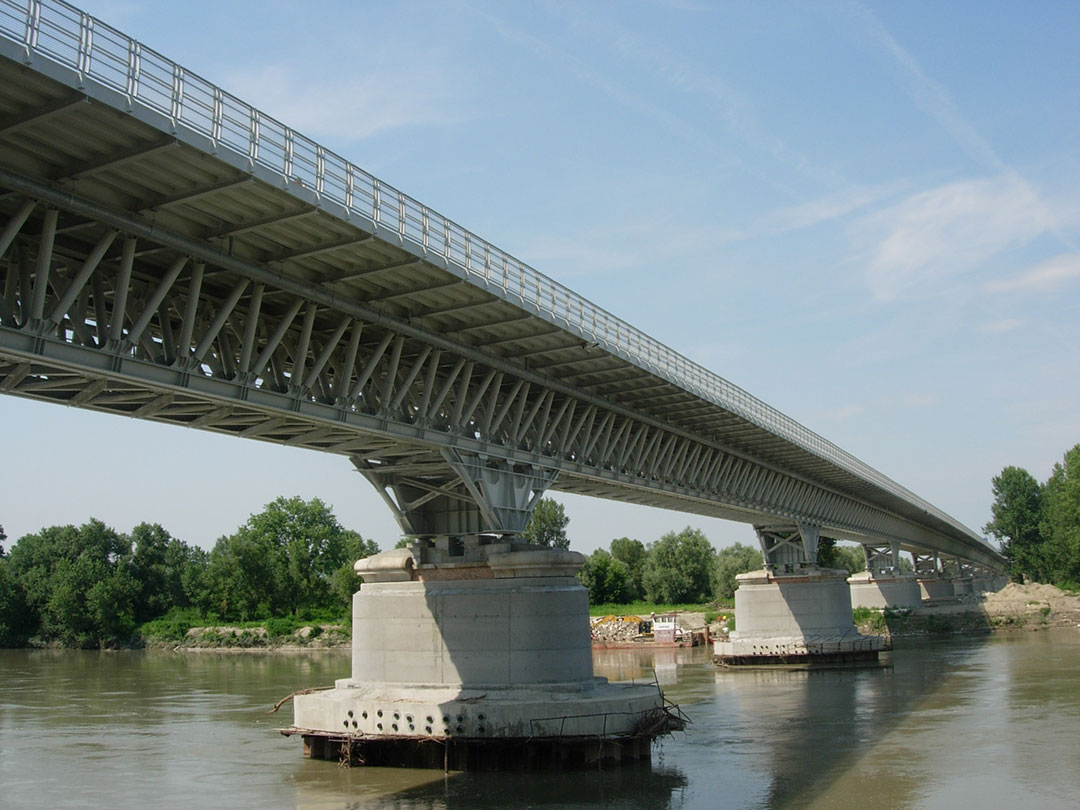
Esempio di ponte a travata reticolare continua su più appoggi: Ponte sul fiume Po – SS9 (2009-2010 – Piacenza, luce tot: 810 m, campata max: 76 m)
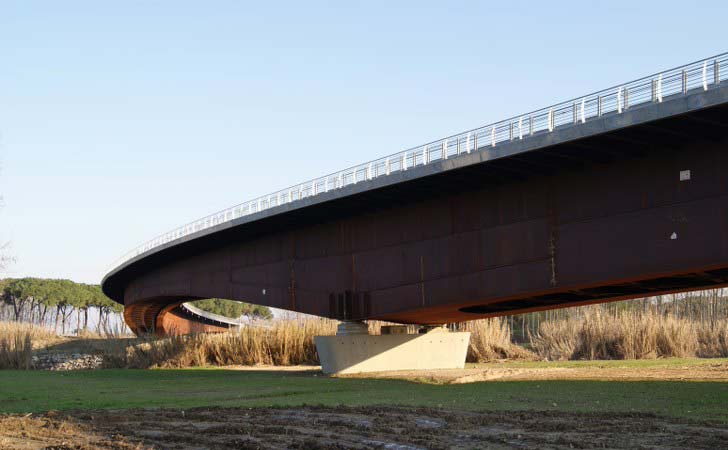
Esempio di ponte con impalcato a cassone monocellulare: Ponte sul fiume Arno (2009 – Pontedera PI, luce tot: 320 m, campata max: 160 m)
I ponti a telaio possono avere differenti conformazioni a seconda dell’uso, e sono formati dai collegamenti resistenti a flessione denominati traversi di telaio e dagli elementi verticali d’appoggio chiamati ritti di telaio. Nei casi in cui si ricorre a ritti inclinati, ad esempio per viadotti alti su valli, lo schema strutturale prende il nome di ponte a cavalletto, nel quale si genera un meccanismo di compressione sul traverso di telaio.
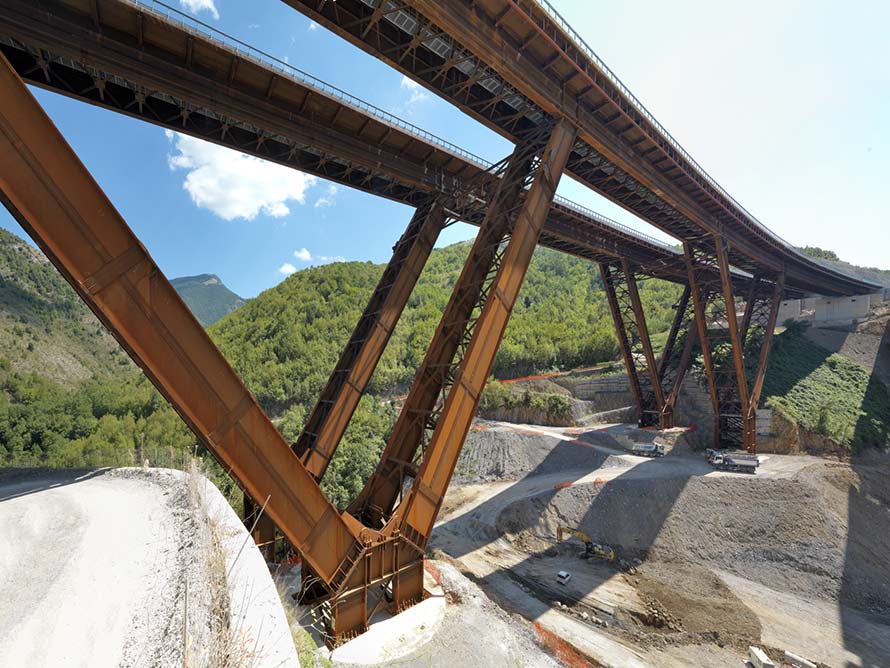
Esempio di viadotto a doppio cavalletto: Viadotto Caffaro (2011-2015 Lauria PZ, luce tot: 399 m, campata max: 139 m)
Ponti ad arco
Lo schema ad arco è stato fra i primi sistemi ad essere utilizzato nel corso della storia, poiché sfrutta il semplice meccanismo resistente a compressione dei materiali da costruzione.
È possibile distinguere due differenti schemi ad arco: ponti a via (o impalcato) superiore e ponti a via inferiore.
I ponti a via superiore sono così denominati perché l’impalcato è collocato in sommità: il tracciato può dunque seguire l’andamento altimetrico dell’arco oppure mantenersi pressoché costante grazie all’utilizzo di elementi verticali denominati piedritti, i quali hanno la funzione di trasmettere alla struttura ad arco i carichi provenienti dall’impalcato. In questo schema, le sezioni di imposta dell’arco devono necessariamente assorbire consistenti spinte orizzontali in aggiunta a quelle verticali. Solitamente questo tipo di meccanismo resistente viene utilizzato in presenza di terreni rocciosi ed è molto utile soprattutto per superare vallate, quando la via di comunicazione si trova ad una quota superiore rispetto al fondovalle.
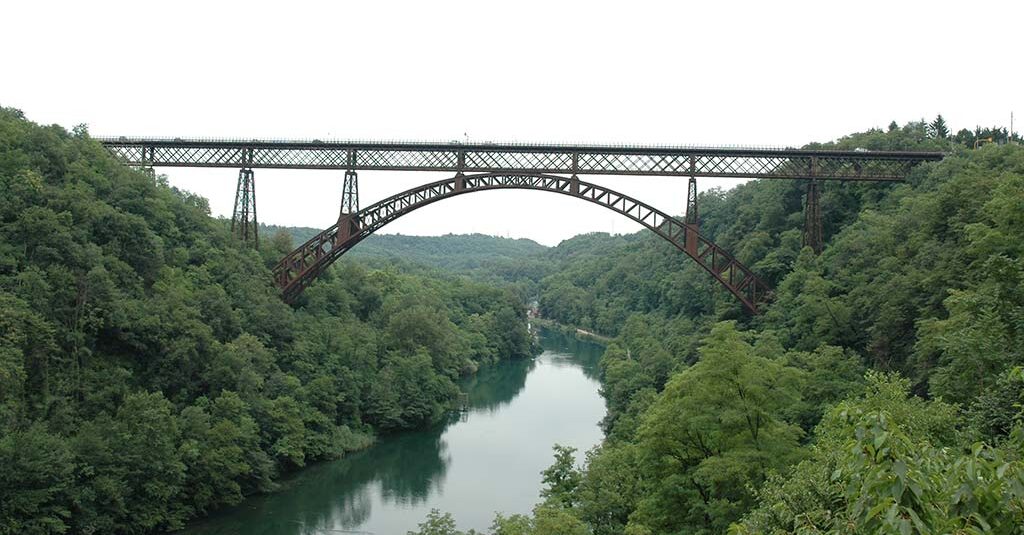
Esempio di ponte ad arco a via superiore: Ponte San Michele (1887-1889 – Paderno d’Adda, luce tot: 266 m, campata max: 150 m)
I ponti a via inferiore sono formati da un impalcato in posizione sottostante che risulta appeso tramite pendini alla struttura superiore ad arco. Questo schema resistente elimina la spinta orizzontale dell’arco mettendo in tensione l’impalcato e viene infatti utilizzato in quei casi in cui l’entità delle spinte risulti incompatibile con le strutture di fondazione o le caratteristiche del terreno. Questa tipologia prende anche il nome di ponte ad arco a spinta eliminata.
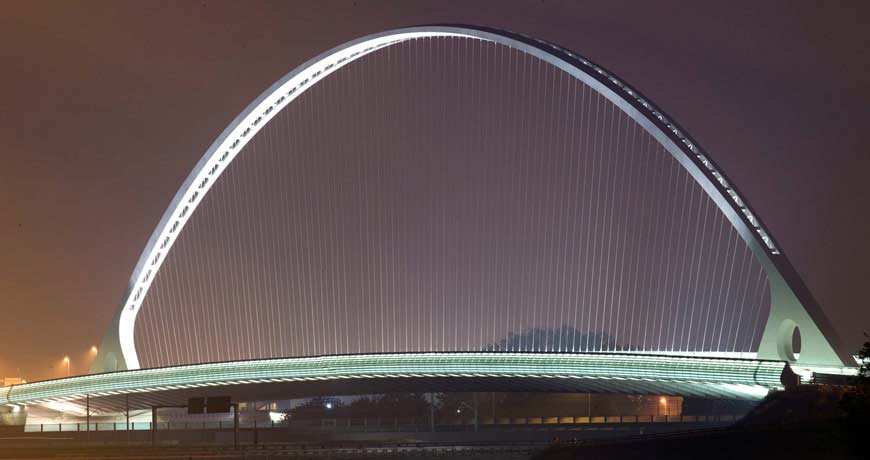
Esempio di ponte ad arco a via inferiore: Cavalcavia Autostrada A1 e TAV (2006 – Reggio Emilia, campata max: 221 m)
Ponti strallati
I ponti strallati sfruttano il meccanismo resistente assiale degli elementi. Il peso dell’impalcato è trasferito alle antenne (torri compresse) attraverso gli stralli (cavi tesi), i quali ne costituiscono l’elemento caratterizzante. Gli stralli trasmettono con una certa angolazione i carichi provenienti dall’impalcato alla sommità delle torri.
L’antenna, a sua volta, scarica verticalmente il carico alla pila e dunque al suolo sfruttando il meccanismo resistente a compressione. Per evitare che vi sia flessione lungo le torri è necessario che la risultante delle forze provenienti dagli stralli coincida con l’asse dell’antenna stessa. Esistono varie tipologie di antenna: la configurazione con antenna centrale prevede l’utilizzo di un impalcato di tipo torso-rigido, quella ad “H o doppia I”, in cui le antenne sono disposte sui lati, affida gran parte della rigidezza torsionale alle due file di stralli, mentre quelle ad “A” o “λ” , nelle quali le antenne ai lati si ricongiungono in sommità, garantiscono minori oscillazioni torsionali grazie alla collaborazione degli stralli e contemporaneamente possiedono una migliore resistenza alle sollecitazioni trasversali.
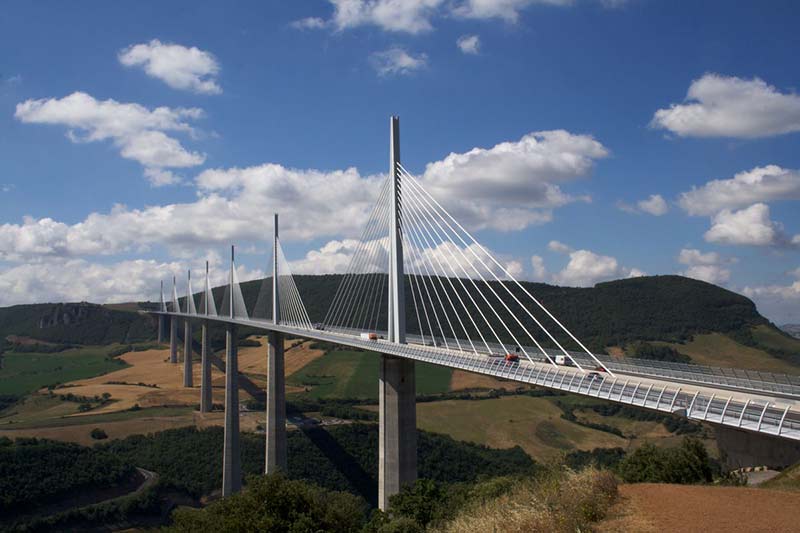
Esempio di ponte strallato con antenna centrale: Viadotto di Millau (2001-2004 – Millau, Francia, luce tot: 2.460 m, campata max: 342 m)
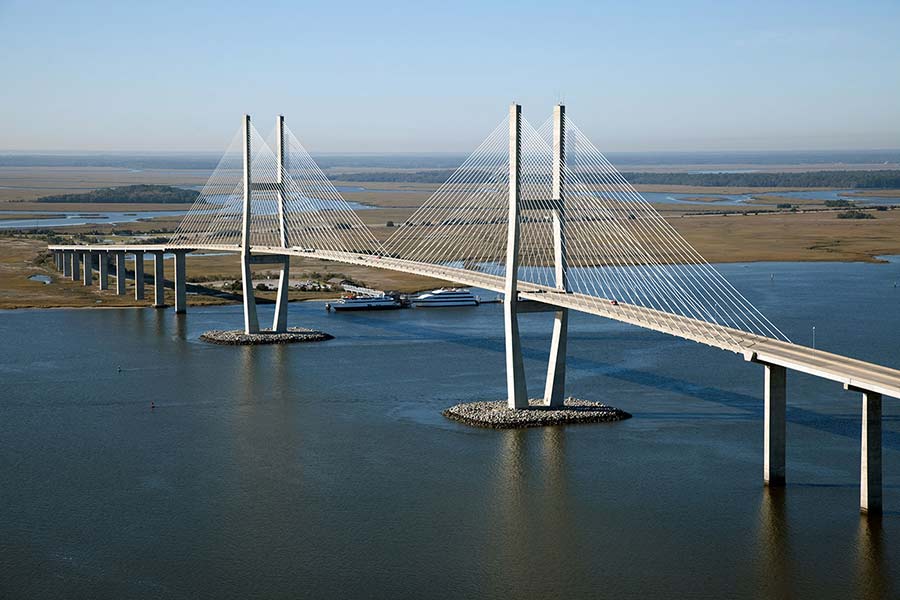
Esempio di ponte strallato con antenna ad “H”: Sidney Lanier Bridge (2003 – Brunswick, Georgia, USA, luce tot: 2.371 m, campata max: 381 m)
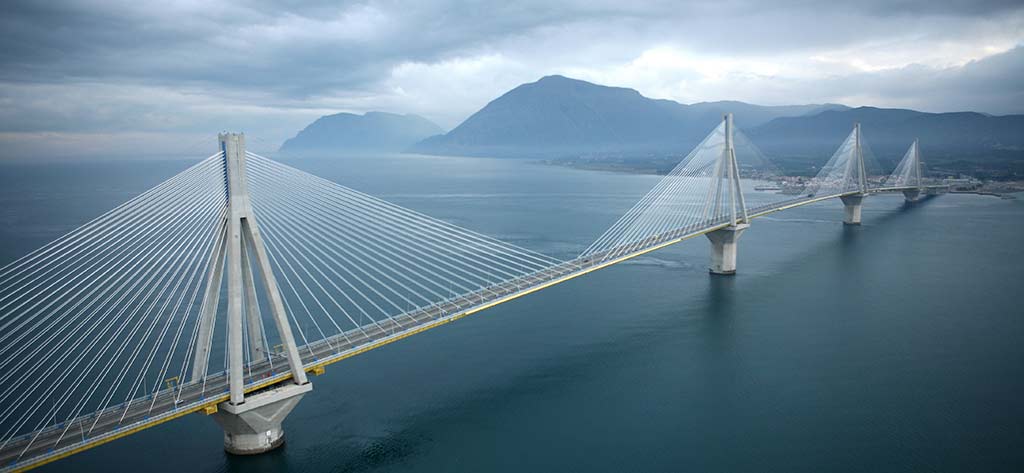
Esempio di ponte strallato con antenne a “λ”: Rion Antirion Bridge (1999-2004 – Golfo di Corinto, Grecia, luce tot: 2.883 m, campata max: 560 m)
La disposizione degli stralli sulle antenne è determinante sul rendimento del complessivo schema statico: una disposizione degli stralli “a ventaglio” ottimizza il supporto verticale dell’impalcato, ma riscontra difficoltà realizzative causate dal sovraffollamento dei cavi in sommità e problemi strutturali generati dalla concentrazione degli sforzi; lo schema “ad arpa” evita il sovraffollamento degli stralli, ma ne riduce di gran lunga il rendimento; lo schema “a ventaglio modificato” rappresenta la soluzione costruttiva più bilanciata.
L’inclinazione degli stralli incide in modo crescente sulla compressione dell’impalcato man mano che ci si avvicina alla base delle torri. Questa caratteristica ne limita l’uso per luci molto grandi.
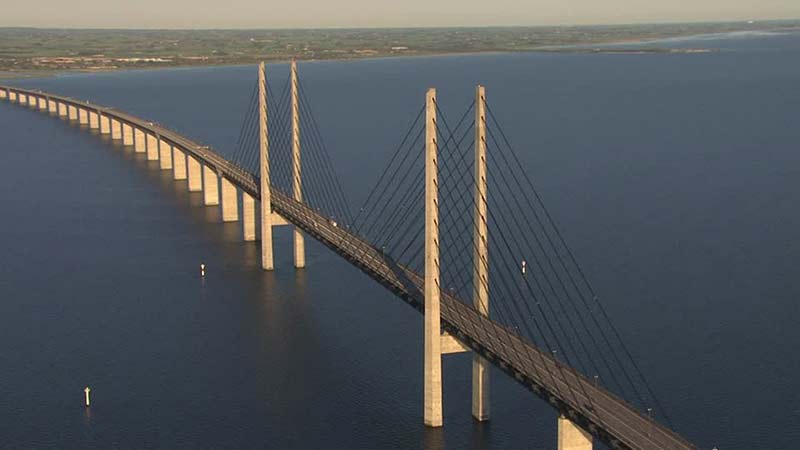
Esempio di configurazione ad arpa: Ponte di Øresund (1995-2000 – Dragør-Malmö, Danimarca-Svezia, luce tot: 15.900 m, campata max: 490 m)
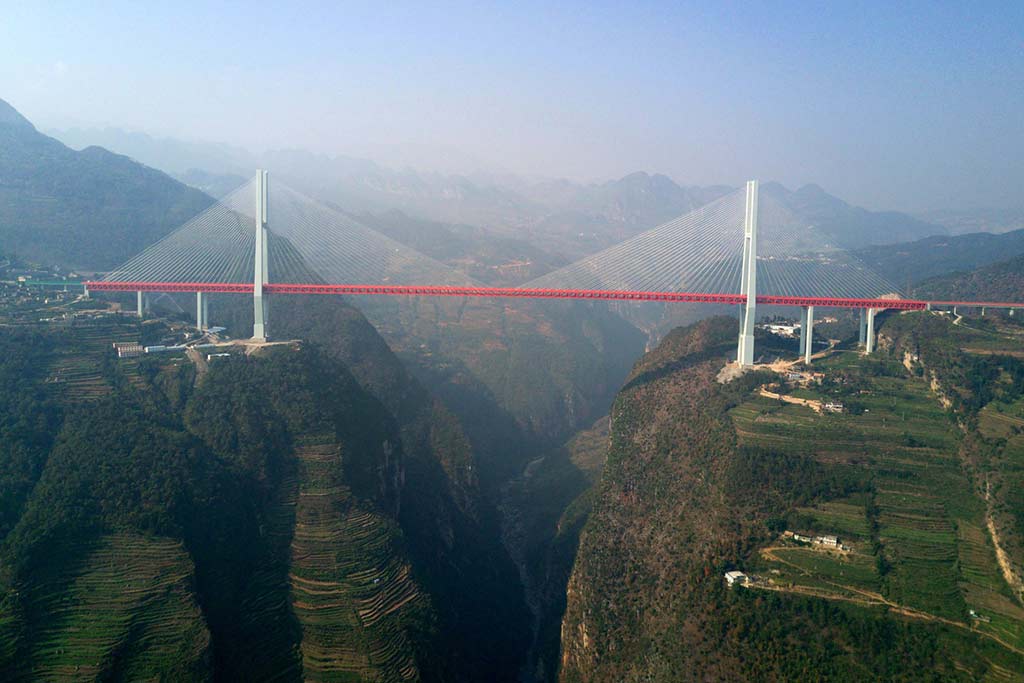
Esempio di configurazione a ventaglio modificato: Beipanjiang Duge Bridge (2016 – Liupanshui, Cina, luce tot: 1.340 m, campata max: 720 m)
Ponti sospesi
Questa tipologia è utilizzata per coprire le luci maggiori, poiché sfrutta interamente il meccanismo resistente assiale degli elementi. L’impalcato è sorretto da cavi verticali denominati “pendini” (schema ad appoggio elastico), i quali trasferiscono verticalmente il peso solitamente ad una coppia principale di funi. Ciascuna fune, correndo da una sponda all’altra, è ancorata a terra e trasferisce il carico proveniente dai pendini alle torri (pennoni). In questo modo si evita di creare compressione nell’impalcato, trasferendo a terra le spinte orizzontali. In caso non sia possibile trasferire a terra le spinte orizzontali è possibile ancorare le funi direttamente all’impalcato, generandovi tuttavia sollecitazioni di compressione. Per evitare inoltre che sul pennone si formino sollecitazioni di tipo flessionale, si consente alla fune di scorrere in sommità, adattandosi ai carichi variabili agenti.
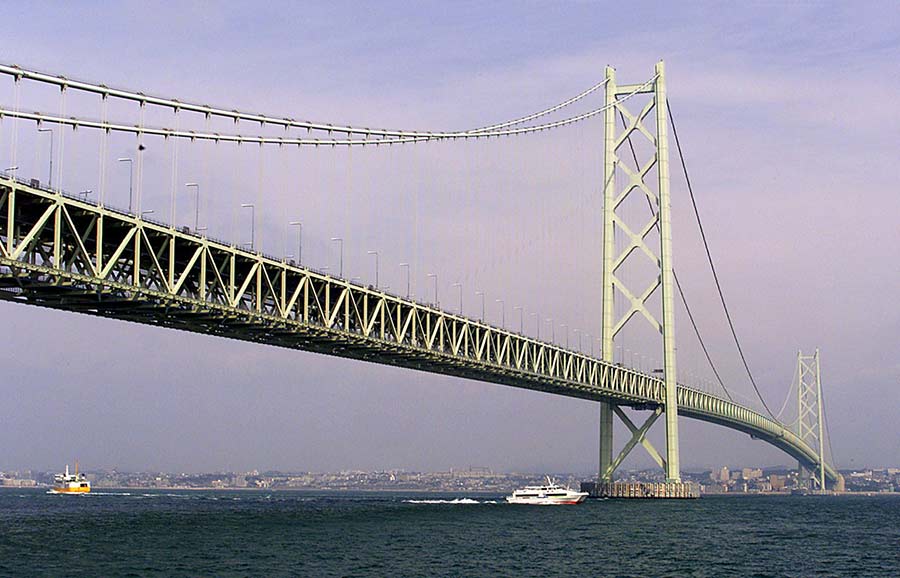
Esempio di ponte sospeso: Akashi Kaikyo Bridge (1988-1998 – Kobe, Giappone, luce tot: 3.911 m, campata max: 1.991 m)
Progettazione di ponti in acciaio
01. I prodotti in acciaio per la costruzione di ponti
Prodotti e materiali
Il tecnico che si occupa della costruzione di ponti e viadotti in carpenteria metallica ha la possibilità di utilizzare una vasta gamma di prodotti che si possono distinguere nella pratica in due tipi di approcci, basati rispettivamente sulla composizione chimica e sul processo produttivo.
Dispositivi di vincolo
Gli appoggi hanno normative armonizzate di riferimento ossia sono coperti da marchio CE in accordo con le relative parti della normativa europea EN 1337.
02. Soluzioni di impalcato per ponti in acciaio
03. Soluzioni per solette negli impalcati misti acciaio-cls
Approfondimento dedicato ai principali aspetti costruttivi delle diverse soluzioni per le solette tipicamente installate per gli impalcati a sezione mista acciaio-calcestruzzo: solette in lastre predalle, solette prefabbricate in c.a., solette a lastra mista acciaio-cls e soluzioni a lastra ortotropa.
La costruzione di ponti in acciaio
La realizzazione dei ponti in acciaio avviene attraverso fasi ben delineate e organizzate che ottimizzano a livello economico il loro processo di costruzione, dalla progettazione e approvvigionamento del materiale alla messa in opera.
Realizzazione dei manufatti in officina
Buona parte delle fasi di realizzazione della struttura di un ponte avviene all’interno delle officine dei costruttori metallici.
Generalmente la reperibilità dei prodotti in acciaio che vanno a comporre un ponte in carpenteria metallica, siano essi lamiere, profili aperti o tubolari, si colloca sui 30 giorni per i comuni acciai, mentre per gli acciai autopatinabili i tempi di approvvigionamento sono leggermente maggiori, con quantitativi minimi variabili a seconda del produttore. In caso di laminazioni ad hoc possono servire dai 60 ai 90 giorni.
È possibile approfondire l’argomento sui prodotti da ponte al seguente link:

Le officine di produzione di carpenteria metallica costituiscono un ambiente protetto e controllato avente tutto l’occorrente per la realizzazione dei manufatti, ad esempio dai carriponte agli impianti automatici di saldatura, oltre che al personale qualificato per il controllo della materia prima all’ingresso.
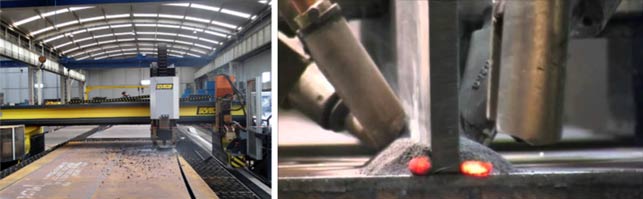
Tutte le fasi di ndustrializzazione, atte a realizzare dei macro-conci facilmente trasportabili, rispondono con precisione ad un piano di fabbricazione ed un controllo che analizza fase per fase tutte le procedure che vanno trattate, sulla base delle principali norme vigenti (per l’esecuzione si fa riferimento alla EN 1090), dal prelievo dei talloni da parte della Direziona Lavori prima della costruzione in officina, al controllo delle saldature da parte di personale specializzato e alla marcatura CE dei componenti strutturali in carpenteria metallica.
I tempi di realizzazione dei manufatti in officina dipendono principalmente dalle dimensioni degli stabilimenti. Come riferimento, un’officina media produce circa 1.000 tonnellate al mese dall’approvvigionamento dei materiali.
Trasporto
Generalmente i macro-conci che escono dalle officine hanno dimensioni standard, che rispondono alle esigenze di trasporto sulla base delle sagome dei principali mezzi, come gli autoarticolati. I volumi di trasporto presentano tipicamente le seguenti dimensioni:
- Larghezza: 2,55 m
- Lunghezza: 16,50 m
- Altezza: 4,00 m
È comunque presente una certa casistica in cui è necessario ricorrere a trasporti eccezionali, arrivando anche ai 24 m di lunghezza.
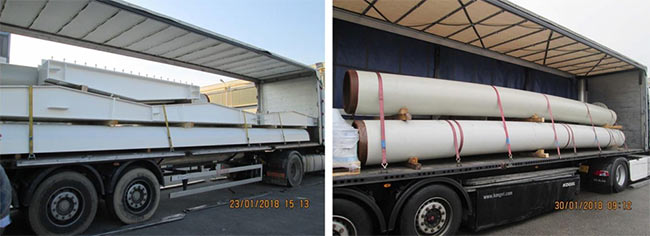
Realizzazione dei trattamenti protettivi
In base al progetto, l’esecuzione dei trattamenti protettivi può avvenire in appositi stabilimenti, soprattutto se è necessaria la zincatura a caldo e/o la verniciatura, o anche direttamente in cantiere, in particolare per la verniciatura a liquido.
Il tempo di realizzazione del trattamento di zincatura a caldo per manufatti consegnati in zincheria può essere calcolato sulla base della capacità produttiva media, che per impianti di grandi dimensioni può raggiungere le 100 t per turno di lavorazione.
Per la verniciatura i tempi medi per 30 t di materiale, tra consegna al reparto del trattamento di verniciatura e carico per il trasporto in cantiere, si attestano sui 10 giorni lavorativi.
È possibile approfondire l’argomento sui trattamenti protettivi per i ponti in acciaio ai seguenti link:
Premontaggio in cantiere
In cantiere viene predisposto uno spazio dove vengono stoccati, in modo idoneo a ridurre i costi di logistica ed in funzione del successivo sollevamento, i conci provenienti dall’officina.
Seguendo i disegni di montaggio, si assemblano i vari componenti, mediante bullonatura e/o saldatura, nel rispetto delle geometrie precostituite in officina, impostando su blocchi (generalmente in calcestruzzo) il profilo dell’impalcato comprensivo delle monte.
In caso di conci solidarizzati mediante saldature a piè d’opera o in quota, generalmente si tende a privilegiare, per ovvi motivi di forza di gravità a cui sono soggetti i bagni fusi di materiale d’apporto, preparazioni di saldatura eseguibili in piano anziché sopratesta. Differente è il caso di saldature eseguite in officina, dove è possibile ruotare i pezzi da saldare ponendoli in posizione in favore di gravità.
Per la saldatura in cantiere è d’obbligo prevedere appositi capanni al fine di ottenere le necessarie condizioni di esecuzione richieste dalle norme, in particolare per la mitigazione di vento, umidità e basse temperature.
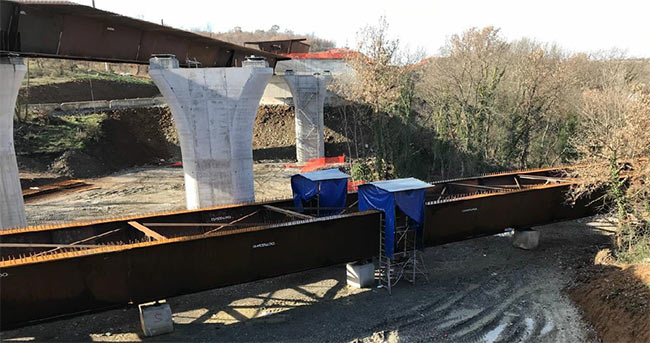
Varo
L’operazione di varo di un impalcato da ponte è l’operazione che consente la messa in opera dell’infrastruttura.
Per i ponti il varo assume un’importante valenza, talvolta dimensionante (soprattutto per i vari a spinta) della parte strutturale.
In funzione della tipologia di ponte e della luce si hanno diversi modi di procedere con il varo: ad esempio, se il ponte ha una campata con luce modesta esso viene assemblato completamente a “terra” e poi posizionato sugli appoggi in calcestruzzo armato, ma per ponti con luci elevate e per schemi statici di travi su più appoggi la carpenteria metallica viene posizionata campata per campata fino al montaggio completo del ponte.
Per eseguire il varo della struttura metallica è opportuno che l’impresa rediga un Piano di Varo, che ha il compito di fornire le informazioni necessarie atte a comprendere le operazioni che porteranno il montaggio delle varie componenti dell’intera struttura.
La scelta della tecnica adottata per eseguire il varo dei ponti dipende da molteplici fattori, fra cui lo schema statico, la luce da coprire, le condizioni orografiche e anche la morfologia dell’ostacolo da superare.
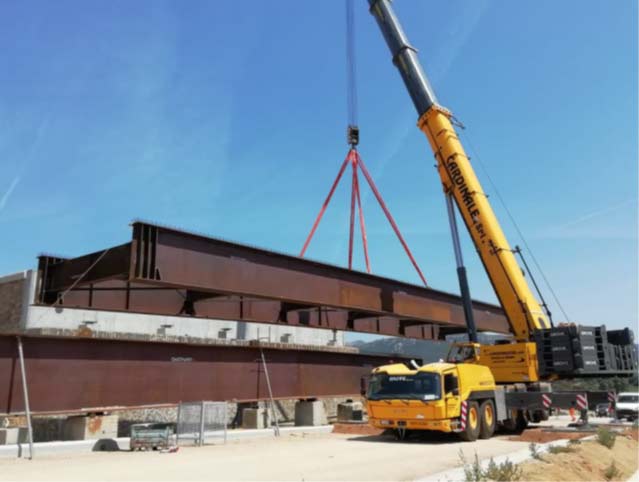
Il varo dei ponti può incidere sensibilmente sugli aspetti progettuali dell’opera, in particolare per quelli strutturali. Esso rende infatti necessaria l’aggiunta di una fase di calcolo strutturale che precede la canonica prima fase di carico classicamente caratterizzata dalla sola struttura in acciaio prima ancora del getto della soletta, ma completa: la fase di varo impone la verifica strutturale delle configurazioni intermedie, che spesso dimensionano talune parti della struttura stessa.
Utili alcune osservazioni su un aspetto essenziale che differenzia totalmente le fasi di costruzione di strutture a sviluppo verticale (grattacieli, torri eoliche, tralicci trasporto energia elettrica, ecc.) da quelle a sviluppo orizzontale o suborizzontale (ponti). Per entrambi i casi facciamo riferimento alle sole azioni gravitazionali.
Il primo caso, apparentemente più ardito, da un certo punto di vista è più semplice in quanto consente di sollevare i componenti strutturali, potendo contare su punti fissi a distanza quasi nulla rispetto alla posizione definitiva. La verticale per il baricentro poco distante dal punto fisso, che può essere anche la parte inferiore di struttura già realizzata.
Il ponte, invece, è una struttura essenzialmente inflessa che permette il collegamento fra due punti altrimenti non consentito per la presenza di una discontinuità o di un ostacolo, come ad esempio l’alveo di fiumi, la presenza di reti ferroviarie e stradali, ecc.
Il baricentro viene a trovarsi proprio al di sopra delle zone spesso inaccessibili che il ponte è chiamato a superare, per cui i punti fissi necessariamente dovranno ubicarsi al di fuori di esse, aprendo pertanto scenari di installazione, o varo, che comporteranno giocoforza metodi ed attrezzature di maggiore impatto rispetto al caso di strutture a sviluppo verticale.
Prendendo in esame caso per caso le condizioni orografiche ed il contesto, si ricorre dunque ad opportune e precise tecniche per il varo, le quali possono essere raggruppate principalmente in due tipologie differenti:
È fondamentale prevedere le tempistiche del varo, comprendendo i posizionamenti delle autogrù e il loro zavorramento, i tempi di sollevamento, spostamento e appoggio della carpenteria metallica sugli appositi appoggi precedentemente preparati soprattutto se vi è la necessità di chiudere al traffico stradale e/o ferroviario per un tempo limitato in favore di un risparmio sui costi di varo.
Posa delle solette d'impalcato
Gli elementi prefabbricati della soletta sono solitamente messi in opera in avanzamento, sia per consentire il conseguente passaggio sull’impalcato del mezzo di posa, sia per ottimizzare la fase di sigillatura e getto di connessione nelle tasche.
Quando le aree di cantiere attorno all’impalcato metallico sono facilmente raggiungibili mediante piste e piattaforme carrabili, gli elementi prefabbricati possono essere sollevati e posati in opera mediante una gru mobile automotrice operante nelle aree suddette.
Nel caso di solette totalmente prefabbricate, gli elementi vengono messi in opera con carri-varo o altri mezzi d’opera o gru mobili tra la zona di consegna degli elementi prefabbricati e le posizioni in opera sull’impalcato. Tali mezzi devono essere in grado di avanzare sia sulle lastre già posate, sia sulle piattabande superiori delle travi principali metalliche in prossimità della zona di posa. Queste macchine possono essere gru mobili o macchine dedicate, costruite specificamente per il cantiere.
Nel caso di lastre prefabbricate a tutta larghezza, vanno verificate con cura le sollecitazioni durante le fasi transitorie di movimentazione e posa, poiché la lastra soggetta al solo peso proprio presenta una sezione resistente per flessione in senso trasversale notevolmente ridotta per la presenza delle tasche di connessione.
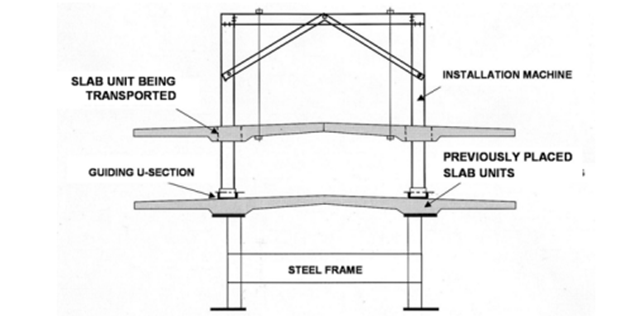
Principi di un macchinario di semplice posa di lastre a tutta larghezza senza rotazione
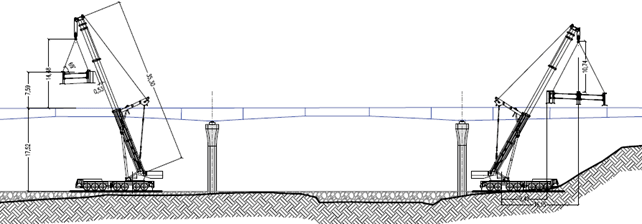
Esempio di sezione di varo con indicazioni delle altezze in fase di montaggio
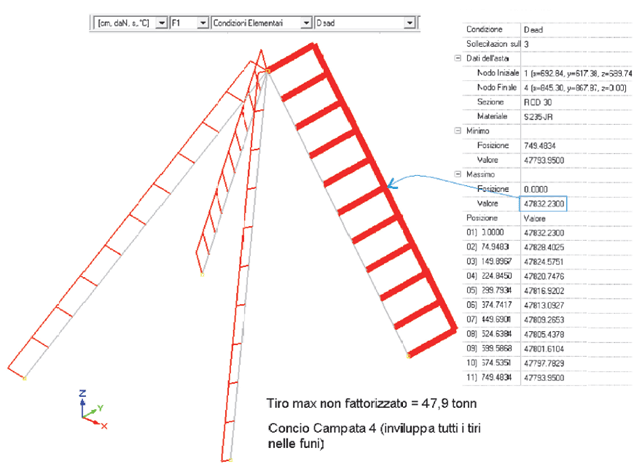
Esempio di modellazione varo per il calcolo del tiro massimo delle funi
La durabilità dei ponti in acciaio
Fra i materiali di largo consumo per la realizzazione di ponti e viadotti, l’acciaio è tra quelli in assoluto più resistenti e durevoli.
Grazie alla scelta di un adeguato sistema di protezione in fase di progettazione è possibile realizzare infrastrutture aventi una vita utile tranquillamente superiori ai cinquant’anni, in alcuni casi anche al secolo, evitando di ricorrere a ripetuti e costosi cicli di manutenzione il che evita lo sperpero inutile di risorse economiche e ambientali.
La scelta consapevole di questi accorgimenti per le infrastrutture si traduce in sicurezza, riduzione dei costi di manutenzione e di gestione ed uso sostenibile delle risorse naturali.
Nel seguito vengono presentati i principali aspetti riguardanti la corrosione, i materiali e i prodotti maggiormente impiegati per la protezione dei manufatti in carpenteria metallica per la realizzazione dei ponti e dei viadotti.
01. Durabilità
La corrosione, i trattamenti protettivi e la durabilità
La corrosione è un fenomeno di graduale deterioramento di un materiale metallico per interazione con l’ambiente circostante. Essa avviene nello strato di umidità (condensa) onnipresente sulla superficie del metallo, spesso non visibile a occhio nudo, secondo processi di ossido-riduzione tra l’acciaio e l’ossigeno atmosferico. La velocità di corrosione viene condizionata da diversi fattori quali l’umidità relativa, l’aumento del tasso d’inquinamento in atmosfera e la concentrazione salina nella condensa.
L’acciaio è un materiale che, per sua natura, è vulnerabile alla corrosione in determinate situazioni, come l’esposizione ad aria umida soprattutto in ambienti molto aggressivi o inquinati. Per contrastarla si può intervenire sulle cause, rendendo l’acciaio meno vulnerabile mediante trattamenti di protezione superficiale o usando materiali in grado di passivarsi, ossia di formare sulla superficie patine di prodotti protettivi compatti e allo stesso tempo sottili.
Il sistema di protezione deve perseguire l’isolamento della superficie del manufatto dall’ambiente esterno aggressivo ed essere in grado di inibire i processi di ossidazione che danno luogo alla corrosione atmosferica.
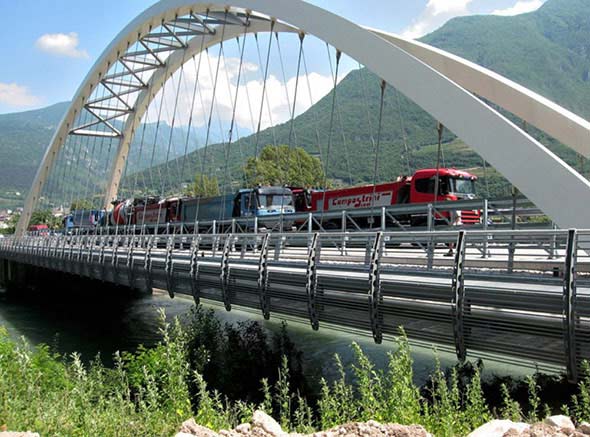
Ponte sul fiume Adige ad Arco (TN)
Ciò, in pratica, viene ottenuto attraverso l’utilizzo di acciaio a resistenza migliorata o all’applicazione all’acciaio al carbonio di trattamenti che comportino un rivestimento della superficie in grado di frapporsi tra l’acciaio e le specie aggressive (effetto barriera o protezione passiva). Per i manufatti a comportamento strutturale vengono applicati dei sistemi polimerici (le vernici) o dei rivestimenti metallici (la zincatura a caldo), seguendo le indicazioni fornite nella UNI EN 1090-2. Si noti che, oltre alla protezione passiva, il rivestimento di zincatura a caldo manifesta anche una protezione di tipo elettrochimico (protezione attiva o catodica).
È ottimale ricorrere a rivestimenti in grado di fornire anche un’azione protettiva di tipo elettrochimico, per ottenere una maggiore affidabilità.
La corrosione, infatti, non è altro che il consumo di elettroni durante il processo ossidativo che porta alla formazione della ruggine (un insieme di ossidi, idrossidi ed altri composti del ferro) per interazione con l’ossigeno atmosferico in presenza di soluzioni conduttive di sali presenti in ambiente. Una contromisura efficace in atmosfera consiste nel fornire continuamente elettroni al metallo da proteggere sfruttando il contatto galvanico con un altro metallo meno nobile, che ossidandosi ceda al materiale di base i suoi elettroni. È ciò che si realizza nel caso del contatto tra zinco (che cede elettroni e si ossida) e ferro dell’acciaio che si mantiene ridotto e, quindi, protetto.
Un criterio guida, essenziale nella scelta del sistema protettivo, deve portare alla massima durabilità possibile in modo da ridurre i costi per le manutenzioni. Il sistema deve essere, praticabile, affidabile, robusto, economicamente compatibile ed ecocompatibile e tale da facilitare le attività ispettive e manutentive, soprattutto nelle parti di difficile accessibilità.
La durabilità dei materiali e della protezione superficiale deve essere garantita dalla corretta scelta dei materiali. Il materiale o il suo trattamento anticorrosivo devono garantire i seguenti requisiti:
- protezione resistente ad urti ed abrasioni;
- protezione attiva (effetto barriera) e passiva (catodica);
- il massimo livello possibile di adesione alla superficie da proteggere;
- protezione anche in caso di superfici chiuse o non ispezionabili;
- protezione per tutta la durata in esercizio del ponte con il minor numero possibile di manutenzioni, cioè in grado di durare per tutta la vita utile dell’opera idealmente senza interventi di manutenzione o riducendone al minimo la frequenza senza alcuna perdita di sicurezza strutturale). Questa indicazione non deve portare alla riduzione della sorveglianza che, al contrario, deve essere garantita con costanza e frequenza delle ispezioni da stabilirsi al momento della progettazione del sistema anticorrosivo al pari delle manutenzioni, per ovviare a danneggiamenti per imprevisti, condizioni locali di particolare aggressività o danni locali alla protezione per qualsivoglia motivo, variazione delle condizioni ambientali di esposizione, errori realizzativi eventuali che possano comportare il non corretto funzionamento in qualche punto del sistema anticorrosivo, ecc.
La scelta del sistema anticorrosivo e la stesura del relativo piano delle manutenzioni deve essere effettuata sin dalle prime fasi progettuali tenendo conto degli ambienti aggressivi, delle opportune misure preventive già individuabili e delle corrette predisposizioni per l’applicazione a regola d’arte della protezione. Occorre favorire metodi e sistemi protettivi applicati in ambienti industriali controllati, piuttosto che demandare la protezione a fasi di cantiere.
Identificazione classe di corrosività
Dopo la definizione della “vita nominale” della struttura, il progettista deve prevedere l’individuazione e la classificazione della corrosività dell’ambiente nella zona in cui la struttura sarà ubicata (secondo la norma UNI EN ISO 9223-2012) e la conseguente identificazione della durabilità dei sistemi di protezione alla corrosione a seconda del tipo di protezione scelta:
- utilizzo di materiale auto-passivante;
- zincatura a caldo, realizzata secondo UNI EN ISO 1461:2009, utili riferimenti si trovano nella normativa UNI EN ISO 14713-1:2017 ed UNI EN ISO 14713-2:2010. Sono disponibili norme relative alla zincatura a caldo che recano una valutazione indicativa del consumo annuale di zinco nelle diverse condizioni ambientali di esposizione;
- protezione mediante verniciatura, la normativa di riferimento è la UNI EN ISO 12944-2:2018.
In tutti i casi, si possono distinguere quattro principali condizioni di riferimento ovvero ambienti di esposizione:
- Rurale: alternanza di umidità e atmosfera secca – assenza pressoché di inquinanti;
- Urbana: alternanza di umidità e atmosfera secca – presenza di diossido di zolfo (SO2);
- Marina: umidità relativamente alta – presenza di cloruri che accelerano la corrosione;
- Industriale: presenza di agenti chimici – livello di corrosione legato al tipo di sostanza inquinante rilasciata nell’aria.
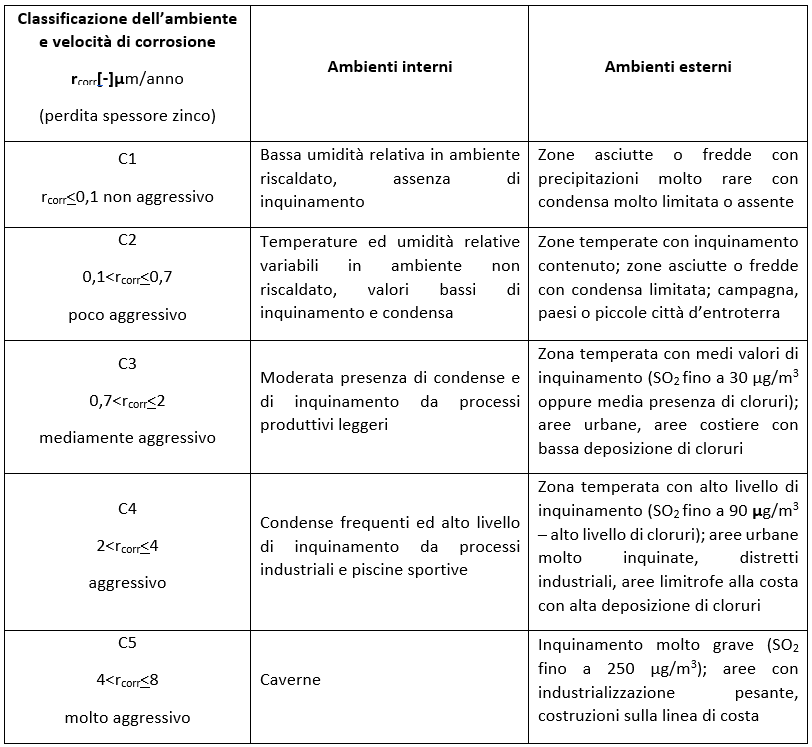
Scelta della classe di corrosività in funzione delle caratteristiche dell’ambiente di esposizione in condizioni tipiche delle zone temperate (tabella ricavata dalla ISO 9223 - Corrosione dei metalli e loro leghe - e dalla UNI EN ISO 14713 – Rivestimenti di Zinco, Linee guida e raccomandazioni)
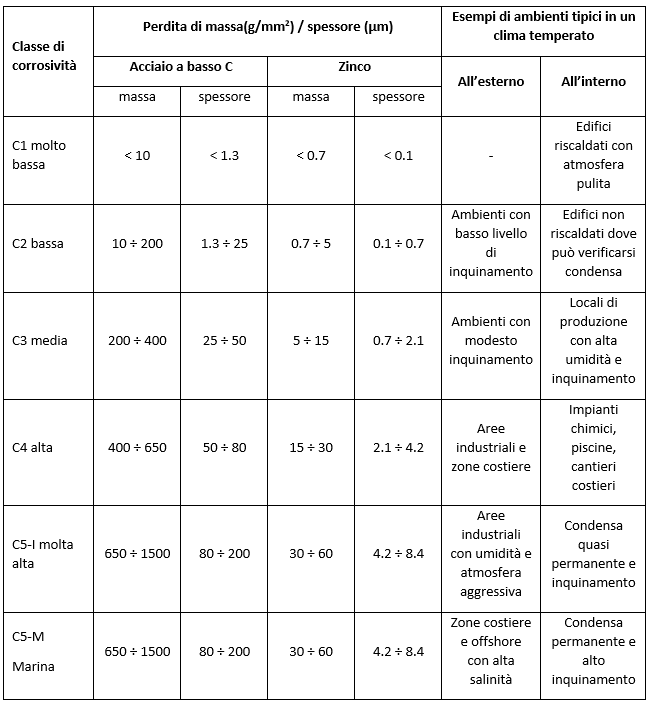
Tabella tratta dalle norme EN ISO 12944-1÷5, Pitture e vernici. Protezione della corrosione di strutture di acciaio mediante verniciatura.
Trattazione a parte merita la gestione degli scarichi risultanti dal dilavamento delle acque particolarmente cariche di cloruri per l’utilizzo durante la stagione invernale del sale di disgelo delle sedi stradali. Detto anche “fondente”, il sale è costituito prevalentemente da cloruro di sodio, cloruro di calcio e dal più costoso cloruro di magnesio. Questi tre composti sono corrosivi e possono determinare il deterioramento del manto stradale, del calcestruzzo e delle strutture in acciaio rivestito o autopatinabile. È utile ricordare che lo ione cloruro per le sue ridotte dimensioni tende a diffondere rapidamente nel calcestruzzo raggiungendo le armature e determinandone l’ammaloramento dell’impalcato in carpenteria, altera le vernici causandone la delaminazione, il contatto con l’acciaio autopatinabile ne destabilizza la patina in modo da renderne il comportamento praticamente indistinguibile dall’acciaio normale non protetto, nell’acciaio zincato a caldo può accelerare la corrosione dello zinco. Sono in commercio anche inibitori di corrosione che possono essere additivati per moderare gli effetti sulle strutture metalliche ma gli effetti tossici sull’ambiente consigliano di limitarne l’utilizzo. Ai fini della protezione dalla corrosione, l’utilizzo dei sali fondenti rende ancora più importante, se possibile, progettare in modo che non siano possibili accumuli di acqua sulla superficie delle strutture, che le acque inquinate dai cloruri vengano convogliate in canalizzazioni o gronde resistenti alla corrosione e rapidamente allontanate dalle strutture, e che si consideri una frequenza ottimale di ispezione per intercettare rapidamente eventuali infiltrazioni o inneschi alla corrosione.
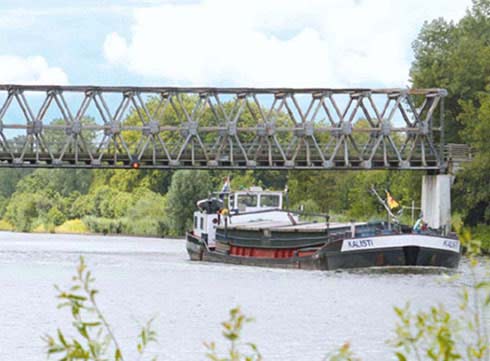
Ponte sul canale Twente ad Ehzer (NL), realizzato nel 1945 in acciaio zincato a caldo
Durabilità
La durabilità è il tempo previsto di durata dell’efficacia di una protezione anticorrosiva fino al primo importante intervento di manutenzione.
La verniciatura protettiva, realizzata secondo UNI EN ISO 12944-5, ha una durabilità molto variabile, in base alla classe del trattamento protettivo e all’ambiente in cui si trova il manufatto metallico, generalmente può durare dai 2 ai 15 anni.
La zincatura a caldo, realizzata secondo UNI EN ISO 1461, determina una protezione di durabilità molto lunga, quantificabile in svariati decenni. A seconda dell’ambiente di esposizione e dello spessore del rivestimento, possono essere facilmente superati i cinquanta anni e, in alcuni casi, anche il secolo senza esigenza di interventi di manutenzione.
Si può considerare un trattamento protettivo anche lo strato di “ossidi” che protegge l’acciaio autopatinabile, esso infatti crea una protezione impermeabile che protegge l’acciaio sottostante anche oltre i 30 anni nelle condizioni ideali di utilizzo.
Si consideri, però, che la valutazione della durabilità, per tutti i materiali e trattamenti protettivi, va effettuata in modo dettagliato se c’è la possibile presenza di punti in cui gli inquinanti, le specie reattive o le soluzioni conduttive, possano determinare un’aggressione localmente più forte. Ciò suggerisce che la protezione dalla corrosione (ovvero, per meglio dire, la sua progettazione) sia prevista in modo da evitare su tutta la superficie del manufatto condizioni che la rendano meno efficiente.
Manutenzione ordinaria
La durata in servizio di una struttura protetta è generalmente superiore alla durata del sistema protettivo adottato. In quest’ottica è necessaria la stesura di un programma di manutenzione, in accordo con l’attuale normativa tecnica, che permetta la fruibilità della struttura per tutto il periodo di servizio di riferimento (vita nominale).
Il programma deve prevedere una manutenzione ordinaria, da tenersi con cadenza regolare per tutta la vita nominale della struttura, a seconda della necessità scaturenti dal particolare trattamento protettivo adottato. È fondamentale che i committenti, la direzione lavori, i costruttori, i realizzatori del rivestimento protettivo e i controllori dei rivestimenti, siano a conoscenza di informazioni concise, complete e precise circa il sistema protettivo utilizzato per la struttura, in modo da permettere a tutti i soggetti coinvolti di interpretare correttamente le indicazioni al fine di consentire le verifiche e le successive operazioni manutentive. Colui che realizza il rivestimento protettivo dovrebbe fornire tutte le indicazioni per permettere la stesura del piano di manutenzione ordinaria.
È necessario eseguire un’ordinaria manutenzione al manifestarsi delle tracce della ruggine (per esempio, se si riscontra una presenza di ruggine su più del 5% di una struttura) e appena vengano riscontrate alterazioni del rivestimento protettivo (sfarinamenti, screpolature, vescicamento, danneggiamenti, distacchi, diffusione di prodotti della corrosione all’interno dei rivestimenti, ecc.).
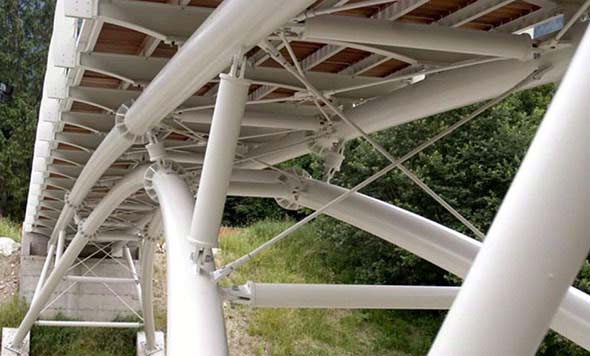
Passerella pedonale con ciclo protettivo combinato zincatura-verniciatura
Ispezione
Per ogni sistema anticorrosivo va stabilita una frequenza di ispezione onde verificare la tenuta del sistema stesso sia globalmente che nei punti in cui possano localmente verificarsi delle criticità o imprevisti (come, ad esempio, inevitabili criticità progettuali, danneggiamenti accidentali, variazione delle condizioni di esposizione).
Anche per trattamenti affidabili e di lunga durabilità come la zincatura a caldo, che in genere non richiede manutenzione se non dopo svariate decadi di esercizio, è consigliabile prevedere delle campagne ispettive a cadenza regolare (per esempio ogni 5-10 anni) per verificare che non ci siamo punti in cui, anche per cause occasionali non prevedibili, possa esserci un consumo anomalo del rivestimento.